The world of printed circuit boards is evolving at a rapid pace. With the introduction of FR-4, a new standard in PCBs has been established.
This new type of board offers improved electrical performance, enhanced thermal resistance, and increased durability. It also provides greater flexibility to designers with its compatibility across multiple platforms and lower production costs compared to previous generations of boards.
FR-4 is set to revolutionize the way that PCBs are manufactured and used in many different industries around the world. From automotive applications to consumer electronics, this innovative material promises greater efficiency for businesses large and small alike.
Its features make it an ideal choice for anyone looking for better reliability with their designs or faster results from efficient manufacturing processes. Whether you’re an experienced designer or just starting in your career, FR-4 is sure to have something that can help you reach your goals quickly and effectively while ensuring quality outcomes every time.
What Even is FR-4

FR-4 is the latest advancement in printed circuit boards (PCBs). It has revolutionized the PCB industry by providing a robust and reliable substrate for electronic components.
This new material consists of a woven glass fabric that is covered with an epoxy-resin compound, usually reinforced with copper foil. FR-4 has become popular due to its superior performance characteristics including high dielectric strength, mechanical strength, excellent thermal stability, and flame retardancy.
Additionally, it can withstand temperatures up to 130°C which makes it suitable for high heat applications. This improved material provides exceptional protection against corrosion and environmental pollutants.
Moreover, FR-4 offers greater flexibility when designing circuits as well as better electrical insulation properties compared to traditional materials like Bakelite or paper phenolic boards. Furthermore, this advanced technology ensures maximum accuracy while manufacturing complex circuitry designs due to its precise dimensional tolerances and low water absorption rate.
This makes FR-4 an ideal choice for those seeking dependable performance from their PCBs at any given time. In conclusion, FR-4 serves as a breakthrough in the world of printed circuit boards by offering increased reliability along with improved design capabilities and durability standards than ever before seen in the industry today!
Properties and Benefits of FR-4

FR-4 is an important advancement in the world of printed circuit boards. It offers a wide range of properties and benefits that other materials cannot match.
Its excellent electrical insulation characteristics, high-temperature resistance, and low water absorption rate make it ideal for use in electronic components. In addition to these features, FR-4 is resistant to corrosion, impact damage, and vibration.
This material also has good mechanical strength which allows it to resist wear caused by frequent contact with metal surfaces or wires as well as any chemical attack from contaminants such as acids or alkalis. The combination of all these properties makes FR-4 the perfect choice for applications where reliability is paramount such as the aerospace industry or medical devices.
It can be used to build complex circuits with intricate designs without compromising on quality or performance. As a result, this type of board ensures maximum safety when used in critical systems like military hardware or mission-critical machines like robotics technology.
Furthermore, its cost-effectiveness compared to other materials makes it attractive for large-scale manufacturing processes too!
Design Considerations When Using FR-4 PCBs
When designing a printed circuit board, it is important to consider the type of material used. FR-4 PCBs are one of the most popular materials in use today due to their cost-effectiveness and durability.
When using an FR-4 PCB, designers should be aware of its limitations as well as its advantages. For instance, FR-4 boards are not suitable for applications that require high temperature or frequency operation.
In addition, they may not provide enough insulation resistance or dielectric strength compared to other types of materials such as polyimide. Moreover, the thickness and size of an FR-4 board must be carefully considered when selecting components since these may affect its performance and reliability over time.
Furthermore, designers should ensure that there is a sufficient air gap between pads on both sides of the PCB to prevent short circuits or crosstalk problems from occurring during fabrication and assembly processes.
Additionally, they need to take into account any potential expansion caused by thermal cycling before committing to a particular design layout with an FR-4 board so that components can be properly mounted without risking damage or failure due to stress over time.
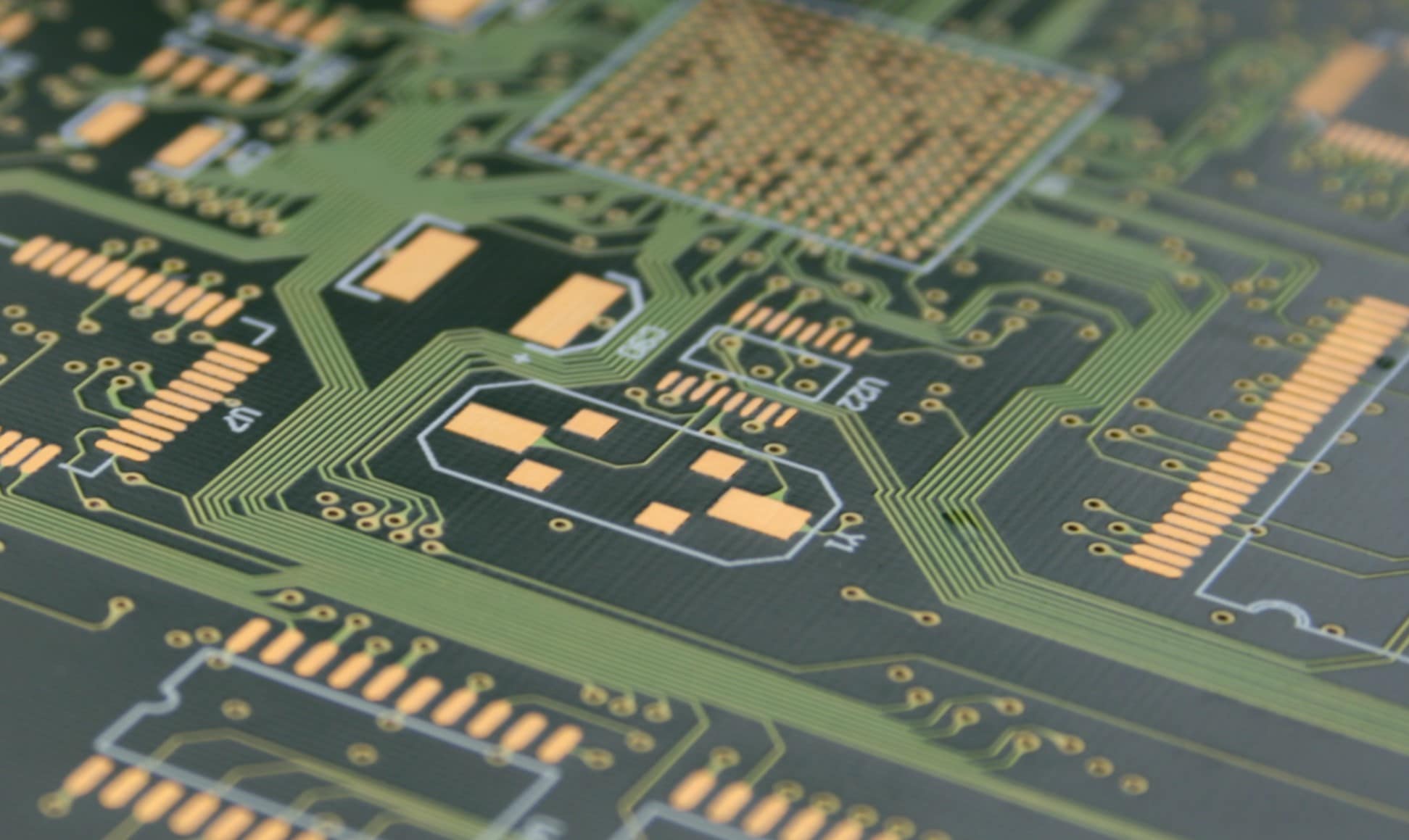
Conclusion
The FR-4 is an innovative new step in the world of printed circuit boards that have opened up a range of possibilities for PCB designers and manufacturers. With its high strength, superior chemical resistance, increased electrical performance, and improved temperature rating, the FR-4 provides greater design flexibility than other materials currently used for printed circuit boards.
The use of FR-4 for PCB represents an exciting breakthrough in technology that will enable more efficient designs with improved reliability and durability. It’s no surprise then that the demand for FR-4 is on the rise, ensuring it will remain one of the most popular choices when it comes to designing Printed Circuit Boards.